Metal Stamping: Advanced Techniques for Achieving Accuracy and Efficiency
Metal Stamping: Advanced Techniques for Achieving Accuracy and Efficiency
Blog Article
Discovering the Globe of Steel Stamping: From Design to Manufacturing
Within the realm of production, steel marking attracts attention as an accurate and efficient method for forming metal sheets into various forms with impressive uniformity. From the preliminary design phase where intricate patterns take shape to the intricate manufacturing procedures, steel stamping is a blend of creativity and engineering. Looking into this globe introduces a complex interaction of imagination and technological proficiency, providing a peek into a realm where technology fulfills workmanship.
Background of Steel Stamping
Metal marking, a widely utilized production procedure today, has an abundant background that dates back to old times (Metal Stamping). The origins of metal stamping can be traced to ancient worlds such as the Egyptians, who made use of marking strategies to embellish fashion jewelry and ornaments with complex styles. With time, metal stamping evolved, with worlds like the Greeks and Romans using it for creating coins and decorative products
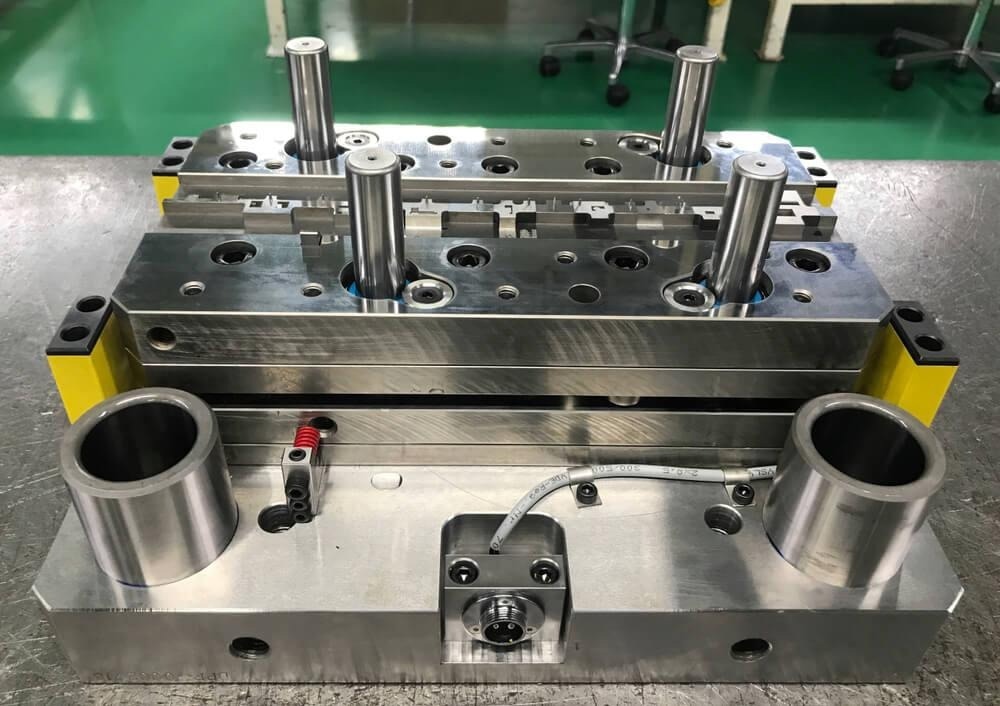
In the 20th century, steel marking proceeded to progress with the combination of automation and computer numerical control (CNC) innovation. These advancements additionally raised the performance and accuracy of steel stamping procedures, making it a vital part of modern-day manufacturing across industries such as automotive, aerospace, and electronic devices. Today, metal stamping continues to be a vital manufacturing procedure, incorporating custom with technology to fulfill the demands of a frequently progressing market.
Design Considerations and Prototyping
When creating metal stamping projects, thorough focus to design factors to consider and prototyping is important for making certain ideal manufacturing outcomes. Layout factors to consider in steel marking include product option, part geometry, tooling design, and manufacturing expediency. Picking the ideal material is vital as it affects the part's efficiency, expense, and manufacturability. Component geometry influences the complexity of the marking procedure and the performance of the final product. Tooling design plays a considerable role in the success of you could try this out steel marking tasks, influencing component accuracy, tool long life, and production effectiveness.
Prototyping is an important phase in the steel stamping procedure that allows designers to evaluate the style, confirm manufacturability, and make necessary changes prior to full-scale production. By meticulously thinking about design aspects and making use of prototyping, manufacturers can simplify the metal imp source marking procedure and accomplish top notch, economical production outcomes.
Tooling and Devices Essentials
Taking into consideration the critical duty that tooling layout plays in the success of metal marking jobs, recognizing the important devices and equipment needed is extremely important for achieving effective production end results. Tooling is an essential element of metal marking, as it straight impacts the quality and uniformity of the end products. Important devices include passes away, punches, and components, which are custom-made to form and form the metal right into the desired parts. Dies are the key tool made use of to cut and create the metal, while strikes help develop holes or certain forms. Components hold the metal in area during the marking process, guaranteeing precision and repeatability. Additionally, devices such as stamping presses, feeders, and coil handling systems are essential for automating the marking process and increasing performance. Investing in premium tooling and tools not just improves manufacturing performance however also leads to greater precision, minimized waste, and total Full Article price financial savings in metal stamping procedures.
Production Process and Quality Assurance
Efficiently managing the manufacturing process and carrying out durable top quality control procedures are necessary for ensuring the success of metal stamping jobs. The manufacturing procedure in steel stamping entails a series of actions that need to be meticulously worked with to attain optimum outcomes.
Quality control in steel marking is critical to deliver items that satisfy the called for specs. By preserving rigorous high quality control requirements, manufacturers can maintain their reputation for supplying top notch steel marked products.
Applications and Sector Insights
In the realm of metal stamping, the effective application of production processes and high quality control actions directly affects the effectiveness and reliability of various industry applications and gives beneficial insights right into the industry's functional dynamics. Additionally, steel stamping promotes the manufacturing of various house home appliances, including refrigerators, cleaning devices, and stoves, by providing cost-efficient remedies for making long lasting and complicated parts. Recognizing the applications and sector insights of steel marking is vital for enhancing manufacturing procedures and enhancing item top quality across various markets.

Final Thought
Design factors to consider, prototyping, tooling, devices, manufacturing processes, and high quality control are important facets of metal marking. With its widespread applications and sector understandings, steel marking continues to be a versatile and reliable manufacturing procedure.
Report this page